Ultrapure Filtration for Semi Conductors
- Feb 24, 2020
- 2 min read
Updated: Oct 20, 2020
Did you know that your phone, tablet or laptop has a "brain"? This "brain" is a semiconductor chip. Semiconductor operations probably require the cleanest chemicals, and the most pure gases of any industry. Consequently, the manufacturing operations are very filtration intensive.

Imagine a semiconductor chip as a major six-lane highway where electrons are flowing. As devices race to become thinner and lighter, rapid advancements in chip design mean that electrons are now travelling on lanes that are only nanometers wide. Reality is, just one 10 nm particle can block traffic and prevent electrons from flowing freely.
This is why the industry has very stringent rules. For example, operators must follow an elaborate “gown up” procedure before entering a cleanroom, and cannot enter a cleanroom immediately after smoking. The cleanliness of the operations directly impacts yield (the % of product that is not rejected and can be sold), and so the benefits of good filtration are very tangible.
Ultrapure/DI water is highly filtered deionized water and does not contain any electrolytes. It is used in large volumes throughout the semiconductor manufacturing process. The specifications for the DI water quality have become increasingly stringent over the years and the filter technology has evolved to meet these requirements.
Filters used to produce ultrapure water must do the following:
• Have low levels of extractables so the filter does not introduce contamination into the water system
• Rinse-up with minimal water flow to 18 megohm-cm resistivity and single digit ppb TOC
• Final filters must be integrity tested/testable to assure performance at the stated micron rating
• Perform consistently from lot to lot
• Must retain captured contaminant even as differential pressures increase and not shed any media
• Be produced in a clean environment or cleanroom
This chart illustrates a typical setup for Ultrapure water filtration, and our recommended product selection in blue.
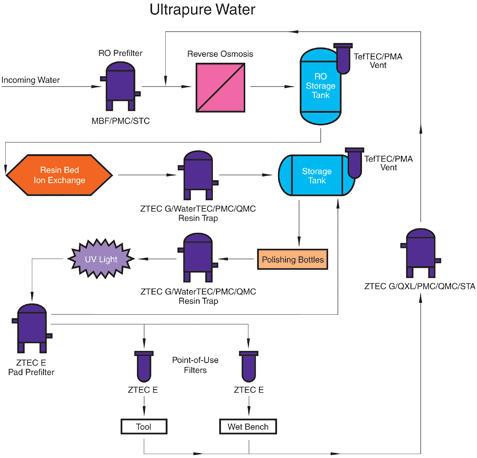
MBF™, STC™, or PMC™: For pre RO applications, depth filters provide effective removal of sediments and particulates to prevent fouling of the RO membrane. 5 micron is most commonly used but finer filtration may be required based on water quality. For longer filter life, the pleated PMC series can be considered.
ZTEC™ G or WaterTEC™, PMC™ or QMC™ DI resin trap: membrane or finely calendared melt blown filters trap any ion exchange resins that may be released from the resin bed. 0.2 or 0.45 micron recommended.
ZTEC™ E Pad prefiltration: Highly consistent membrane filters provide protection of final point-of-use filters
ZTEC™ E Point-of-use cold DI: 0.03 micron ZTEC or 0.05 micron VTEC provide highly consistent performance at this critical process step
TefTEC™ Tank vents: hydrophobic PTFE membrane filters are recommended as tank vent filters to prevent the ingress of particulate or microbes into the stored water tanks. If a more economical solution is desired, consider use of PMA absolute rated pleated polypropylene filters.
ZTEC™ G, QXL™, PMC™, QMC™, STA™: For recycling water after the tool, select the appropriate filter based on contaminants present in the water, before returning water to the DI process.
Contact us to find out more.
Comments